Jump to section
Traditional MES legacy systems were built for stability and meant to last, which is an advantage, but they typically fail to keep up with fast-paced, complex market demands and disruptions of today’s world. Next-gen MES solutions were designed to pick up the slack where legacy systems fall short and support frontline operators with the tools they need for faster time-to-market.
What Does a Manufacturing Execution System do?
Broadly speaking, MES are responsible for managing resources, scheduling production, coordinating execution, and collecting production data, among many other applications.
What Does a Next-Generation MES / Frontline Operations Platform do?
An operations platform is a connected data and process management tool that connects people, things (machines and devices), and systems used in a production or logistics process in a physical location.
As previously noted, the manufacturing industry has dramatically changed operationally, technically, and socially, which is affecting the way manufacturers do business, impacting traditional MES in the following ways:
Blurred tech stacks
Increased cloud adoption
Workforce transformation
Increased disruptive events out of our control
Connecting devices at the edge is more important
Therefore, whether you’re a manufacturer looking to transition from a legacy MES to a next-gen MES, or adopt a new frontline operations platform altogether, you’ll need to consider some key areas that will determine if an implementation will be successful.
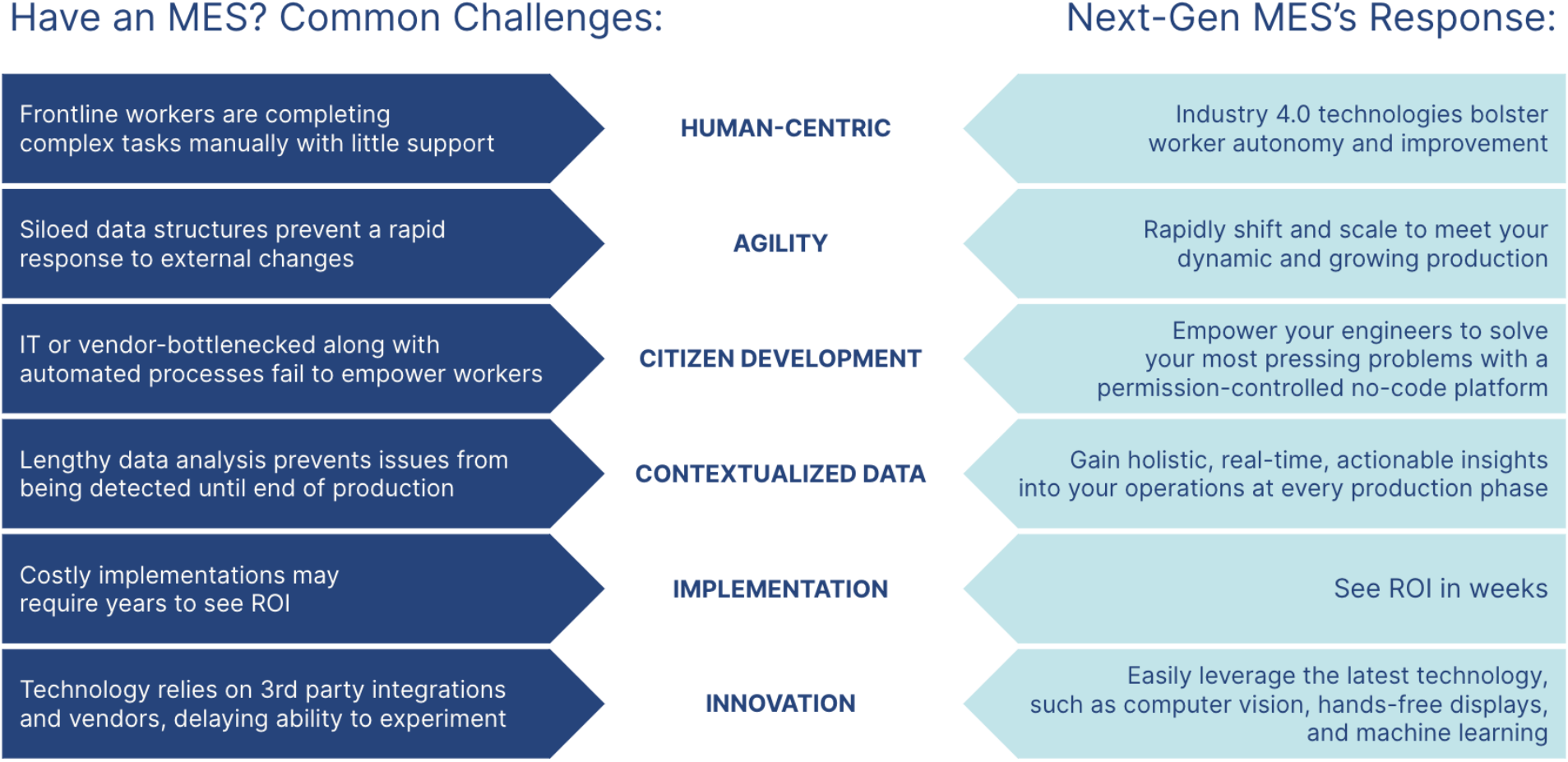
Human-Centric
When equipping frontline workers with a new next-gen system, manufacturers should consider user acceptance and experience and ask themselves:
How easily will users accept and be able to adopt the system?
What is the experience like for end users that need to interact with the system?
Can you reliably collect data from humans in a standardized way?
Is there a way to improve efficiency and error-proof tasks?
Under a legacy MES, frontline workers struggle to complete complex tasks manually with little support, increasing the chance of errors and frustration. Frontline operations platforms, on the other hand, apply industry 4.0 technologies to bolster worker autonomy and improvement.
Agility
When planning an agile and low risk deployment, manufacturers should ask themselves:
How long should I wait to get value from my MES?
Our process and product will continue to evolve. How will my system evolve with me?
How do I accommodate every need, over time?
How do we plan this journey and where do we start?
A traditional MES is limited to siloed data structures and a top-down hierarchy that restrict rapid response to external changes, limiting an organization’s ability to compete. By contrast, a next-gen MES system rapidly shifts to meet your dynamic and growing production, allowing you to scale as you go and implement inexpensive pilot programs that suit your specific needs.
Citizen Development
When considering ways to remove IT bottlenecks and reliance on vendors, it’s important to ask:
How much should I rely on my IT team to support my manufacturing operations?
What is the ratio of Software to Services?
Do you do your homework to anticipate how your MES needs will grow/change over time?
Traditional MES rely on IT or vendors and use automated processes that fail to empower workers. With a frontline operations platform that uses no-code tech, manufacturers augment their engineers and operations staff with the tools they need to solve their most pressing problems.
Contextualized Data
When developing a system for flexible, accessible and contextualized data, consider the following:
What information do you need to get a holistic view of operations?
How easily can you add new data sources (via sensors, machines, cameras, etc.)?
Can you reliably collect data from humans in a standardized way?
Are you able to take action in real-time based on the data you are collecting?
A downside of traditional MES is that they usually involve lengthy data analysis that prevents issues from being detected until the end of production. As such, product defects go undetected until it’s too late and it becomes a problem. Fortunately, a next-gen MES allows manufacturers to gain holistic, real-time, actionable insights into their operations at every phase of production, facilitating the identification of issues as they arise.
Innovation
When executing a strategy meant to support innovation within your organization, it’s critical to ask the following:
How can you achieve faster time-to-value?
Do you have the proper environment set up to foster creativity and collaboration?
Are your frontline operations teams equipped with the proper tools to experiment?
Is your operation designed with compliance regulations in mind?
Technology that relies on third party integrations, vendors, and IT, is not conducive to innovation because it disempowers frontline operations workers by creating data silos and bureaucracy that gets in the way of developing breakthrough solutions to existing problems. With a next-gen MES system, engineers and operators can leverage the latest, cloud-based technology with no coding expertise, enabling their collective ability to experiment, manage permissions, streamline complex actions, and comply with regulatory requirements.
Implementation
When implementing a pilot for a next-gen MES, here are some questions to think about in order to avoid unnecessary costs:
What are the upfront costs and the ongoing costs?
Are there any additional benefits that you need to consider when comparing the value?
Have you evaluated all of the costs of implementing your system including hardware, implementation, software, ongoing support and maintenance?
With a traditional MES, deploying any updates can be costly and require years to see ROI, discouraging manufacturers from taking the necessary steps to digitally transform their operations. However, with a frontline operations platform, manufacturers can experience ROI in just weeks.
Implementing a new system, process, or almost any new aspect in your production line always involves some level of difficulty, which is why manufacturers need to first identify the critical points, and then build pilots to address these individually. Although full implementation will take time, you’ll be able to see early value by implementing low-risk pilots. These pilots need to be fast, simple, and targeted.
When deciding whether to make the switch to a frontline operations platform, you should challenge your MES vendor with your future change use cases to fully understand the capabilities of your existing MES, while recognizing potential ramifications to your operation. Keep in mind that user acceptance and adoption is crucial in your implementation strategy, so you’ll want to incorporate the feedback of your frontline workforce when evaluating a next-gen MES system.
Automate data collection and improve productivity with Tulip
Speak with a member of our team to see how a system of apps can connect the workers, machines, and devices across your operations.