Définition de l'équilibrage des lignes dans la fabrication
L'équilibrage de ligne est une stratégie de production qui consiste à équilibrer le temps de l'opérateur et celui de la machine afin de faire correspondre le taux de production au temps de cycle.
Le Takt time est le rythme auquel les pièces ou les produits doivent être fabriqués pour répondre à la demande du client.
Pour une ligne de production donnée, si le temps de production est exactement égal au temps de cycle, la ligne est parfaitement équilibrée. Dans le cas contraire, les ressources doivent être réaffectées ou réorganisées pour éliminer les goulets d'étranglement ou les capacités excédentaires. En d'autres termes, les quantités de travailleurs et de machines affectées à chaque tâche de la ligne doivent être rééquilibrées pour atteindre le taux de production optimal.
Avantages de l'équilibrage des lignes
1. Réduire les déchets d'attente
Le gaspillage lié à l'attente est l'un des huit types de gaspillage de la production allégée. Il s'agit de tous les temps morts qui surviennent lorsque les opérations ne sont pas entièrement synchronisées. Par exemple, le gaspillage d'attente se produit lorsque les opérateurs attendent des matériaux ou que quelqu'un d'autre achève leur tâche. Les temps d'arrêt de l'équipement - pendant lesquels l'équipement ne fonctionne pas - sont un autre exemple de gaspillage d'attente.
L'équilibrage des lignes garantit que tous les opérateurs et toutes les machines travaillent ensemble de manière équilibrée. Aucun opérateur ni aucune machine ne doit être surchargé ou inactif. En minimisant les temps d'arrêt, l'équilibrage des lignes réduit les déchets d'attente.
2. Réduire les déchets d'inventaire
Le gaspillage des stocks est un autre type de gaspillage. Il correspond à un excès de matières premières, de travaux en cours (produits non finis) ou de produits finis. Le gaspillage des stocks est le signe d'une allocation inefficace du capital.
L'équilibrage des lignes standardise la production, ce qui signifie qu'il est beaucoup plus facile d'éviter les accumulations ou les stocks excédentaires. En réduisant les temps morts, l'équilibrage des lignes garantit un minimum de travail en cours. Enfin, en rapprochant le temps de production du temps de cycle, il garantit le respect des délais de livraison.
3. Absorber les irrégularités internes et externes
L'équilibrage des lignes réduit les variations au sein d'une ligne de production. Une ligne de production équilibrée est suffisamment stable et flexible pour s'adapter aux changements.
Par exemple, si la demande du client change - ce qui signifie que le temps de cycle change - les opérations peuvent être réalignées rapidement grâce à l'équilibrage de la ligne. Les conséquences des changements apportés à une ligne de production équilibrée sont prévisibles. Il est donc beaucoup plus facile de modifier la ligne pour ajuster la cadence de production.
4. Réduire les coûts de production et augmenter les bénéfices
L'équilibrage parfait des lignes permet aux travailleurs et aux machines de fonctionner de manière parfaitement synchronisée. Aucun opérateur n'est payé pour rester inactif. Toutes les machines sont utilisées au maximum de leur potentiel. En d'autres termes, la main-d'œuvre et la capacité des machines sont maximisées. Une telle efficacité des processus se traduit par une réduction des coûts et une augmentation des bénéfices.
Comment parvenir à équilibrer les lignes ?
1. Calculer le temps de cycle
Puisque l'objectif de l'équilibrage des lignes est de faire correspondre le taux de production au temps de production, il est essentiel de connaître votre temps de production. Tulip offre un Takt Time App et un Takt Time Tableau de bord prêts à l'emploi qui font du calcul et du suivi du temps de production une partie intégrante de votre processus de production.
2. Réaliser des études temporelles
Nous avons rédigé un article détaillé sur la manière de réaliser des études de temps. L'objectif des études de temps est de déterminer le temps nécessaire à l'exécution de chaque tâche sur une ligne de production. En d'autres termes, vous voulez savoir combien de temps les employés et les machines consacrent à chaque partie d'un processus.
Gardez à l'esprit que s'il est possible de réaliser des études de temps avec un chronomètre et un presse-papiers, il existe aujourd'hui de bien meilleures options. IoT La connectivité et l'informatique en nuage ont transformé la collecte et le stockage des données. Grâce aux capteurs et aux applications de fabrication, les fabricants peuvent désormais réaliser des études de temps automatiques et continues, éliminant ainsi les biais humains et l'effet de taille de l'échantillon.
3. Identifier les goulets d'étranglement et les capacités excédentaires
Au moment d'analyser les données de vos études de temps, remarquez quelles parties du processus prennent plus de temps que le temps takt. Un dépassement du temps de cycle est synonyme de livraisons tardives, de frais d'expédition élevés ou de clients mécontents. Remarquez également les parties qui prennent moins de temps que le temps takt. Il y a une surcapacité à ces endroits.
4. Réaffecter les ressources
Commencez par tenir compte de la priorité des tâches, c'est-à-dire de l'ordre dans lequel elles doivent être exécutées. Par exemple, si une étape nécessite une certaine partie, vous devez vous assurer que cette partie est terminée avant d'atteindre cette étape. Un diagramme de précédence peut s'avérer utile.
Réorganisez ensuite les tâches afin de réduire les capacités excédentaires et les goulets d'étranglement. Par exemple, déplacez les ressources (travailleurs et équipements) des parties de la ligne qui ont une capacité excédentaire vers les goulets d'étranglement. En d'autres termes, cherchez à alléger la charge de travail là où il y a des goulets d'étranglement et déplacez-la vers des endroits où la capacité excédentaire peut être comblée par l'absorption d'une plus grande quantité de travail. Cela permettra de réduire les déchets d'attente dans les endroits où il y avait une capacité excédentaire. Cela permettra également d'améliorer le flux de production là où il y avait des goulets d'étranglement.
Essayez d'organiser les tâches élémentaires en groupes qui minimisent le temps d'inactivité des opérateurs et qui maximisent l'utilisation des machines et des équipements. Répartissez la charge de travail entre les opérateurs de la manière la plus logique possible, en tenant compte des données que vous avez recueillies sur les performances des opérateurs. Idéalement, chaque groupe de tâches devrait être accompli dans le même laps de temps afin de parvenir à une synchronisation.
Déterminez si vous avez trop ou pas assez de postes de travail. L'équilibrage des lignes peut améliorer l'efficacité du processus jusqu'à ce qu'il y ait une surcapacité sur l'ensemble de la ligne. Il peut être avantageux de supprimer des postes de travail ou de combiner des processus.
Lorsque plusieurs opérateurs effectuent des tâches consécutives et travaillent en tant qu'unité, vous devez vous efforcer de réduire le déséquilibre entre les travailleurs et les charges de travail. Une disposition et une répartition correctes des tâches sur les lignes de production permettent de maximiser la production au moment voulu.
5. Apporter d'autres améliorations
L'analyse des données quantitatives de vos lignes révèlera certainement d'autres possibilités d'amélioration susceptibles d'améliorer l'équilibre de vos lignes.
Pour mettre en œuvre l'amélioration des processus, vous pouvez manipuler trois paramètres : le temps de l'opérateur, le temps de la machine et le temps de préparation. Vous pouvez, par exemple, dispenser une formation supplémentaire aux travailleurs qui mettent plus de temps à accomplir une tâche ou faciliter les transitions afin de réduire les temps de changement. Vous pouvez également moderniser les machines ou vous assurer que les opérateurs respectent les procédures opérationnelles standard (POS) de réglage et d'entretien des machines.
De nombreuses pratiques d'allégement peuvent également contribuer à réduire les variations dans vos lignes. Les 5S et le management visuel créent un espace de travail cohérent, réduisant ainsi le temps perdu à chercher des outils et améliorant l'efficacité du processus. Le Poka-yoke, ou contrôle des erreurs, est un processus qui permet de détecter les défauts à un stade précoce, ce qui accroît la cohérence de la production.
Conclusions
L'équilibrage des lignes est un problème d'optimisation qui revêt une grande importance pour l'industrie. En améliorant l'efficacité de leurs lignes, les entreprises peuvent réduire les déchets de la production allégée et dégager plus de valeur.
Améliorez la productivité de vos opérations grâce à Tulip
Découvrez comment vous pouvez réduire les déchets et augmenter l'efficacité de la production grâce à des applications industrielles sans code.
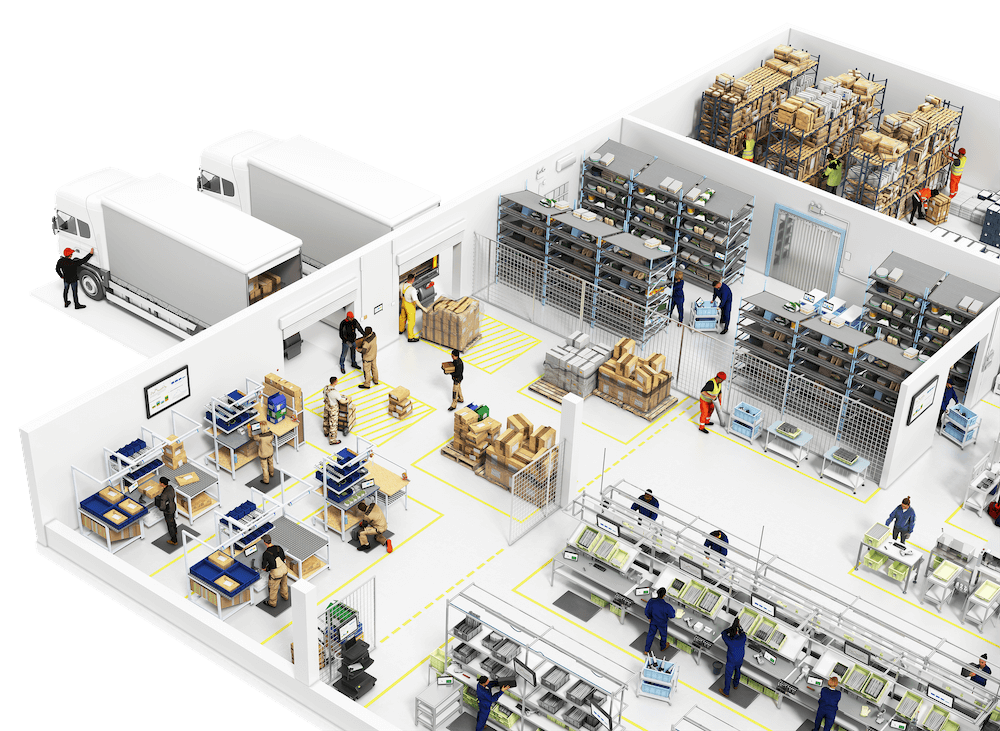